Your cart is currently empty!
Top 5 Common Conveyor System Issues and How to Prevent Them
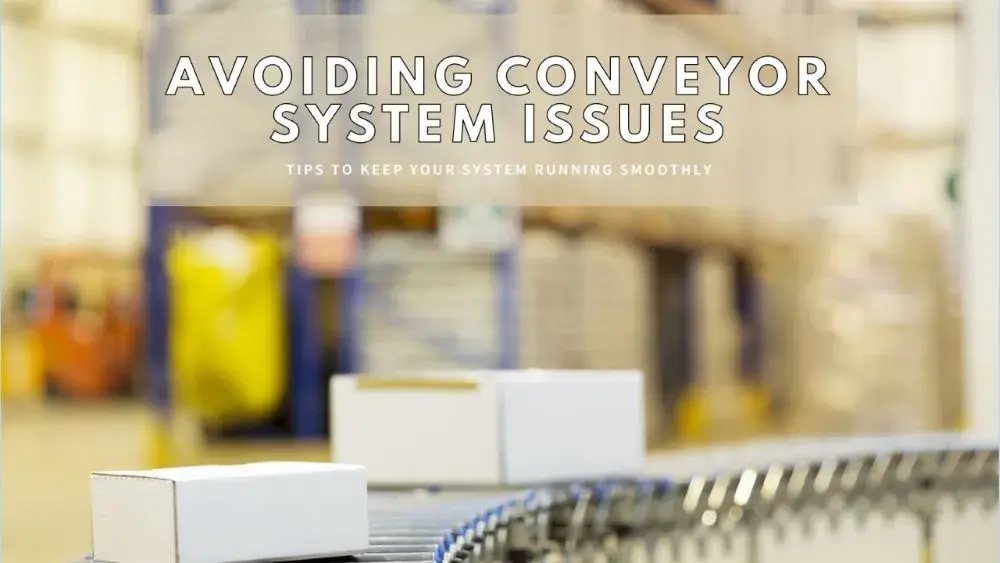
Conveyor systems are the backbone of efficient automotive manufacturing, playing a critical role in streamlining production and enhancing productivity. However, like any complex machinery, conveyors are not immune to issues that can disrupt operations and affect the bottom line. Understanding and addressing these common problems can prevent costly downtime and ensure smooth operation. In this blog post, we will explore the top five common conveyor system issues and provide actionable tips on how to prevent them. Additionally, we will highlight how Omtec’s reliable ball transfers, including pop-up ball transfers and pop-up positioner pads, can significantly enhance your conveyor system’s performance.
1. Belt Slippage
Issue: Belt slippage occurs when the conveyor belt does not move as expected, leading to inconsistent movement and potential damage to the belt and other components. This issue is often caused by improper tension, misalignment, or wear and tear.
Prevention:
- Regular Maintenance: Inspect the belt tension regularly and adjust as needed to ensure proper tension. A belt that’s too tight can cause excessive wear, while a belt that’s too loose can slip.
- Proper Alignment: Ensure that the conveyor system is properly aligned. Misalignment can lead to uneven wear and increased friction.
- Routine Inspections: Check for signs of wear and tear, and replace any damaged components promptly. Regularly clean the belt to remove debris that could contribute to slippage.
2. Mechanical Failures
Issue: Mechanical failures, such as issues with bearings, gears, or motors, can lead to unexpected breakdowns and production stoppages. These failures are often a result of inadequate maintenance or overuse.
Prevention:
- Scheduled Maintenance: Implement a comprehensive maintenance schedule that includes checking and lubricating moving parts, inspecting bearings, and ensuring that gears are in good condition.
- Quality Components: Invest in high-quality components that are designed to withstand the demands of your production environment.
- Training: Ensure that your maintenance team is well-trained to identify potential issues before they escalate into major problems.
3. Accumulation Problems
Issue: Accumulation issues occur when products build up on the conveyor line, leading to blockages and inefficient flow. This problem can be caused by improper spacing, inadequate speed adjustments, or conveyor design flaws.
Prevention:
- Optimize Conveyor Design: Ensure that your conveyor system is designed to handle the expected load and flow of products. Adjust the conveyor speed to match the production rate.
- Use Proper Spacing: Set up the conveyor to maintain appropriate spacing between products to prevent accumulation and ensure smooth flow.
- Monitor Flow: Regularly monitor the flow of products and make adjustments as needed to avoid bottlenecks.
- Omtec ball transfers, such as the PBT-1 pop-up ball transfers, are designed to provide smooth, consistent movement of products. By facilitating even load distribution, these transfers help ensure that no single part of the conveyor system bears excessive weight, thus reducing the risk of overloading.
- Benefit: Even load distribution helps prevent localized stress on the conveyor components, which can lead to premature wear and potential failure. This balance improves the lifespan of the conveyor system and maintains optimal performance.
4. Overloading
Issue: Overloading occurs when the conveyor system is subjected to weights beyond its design capacity. This can lead to excessive wear, mechanical failures, and safety hazards.
Prevention:
- Know Your Limits: Understand the maximum load capacity of your conveyor system and adhere to it strictly.
- Distribute Loads Evenly: Ensure that loads are evenly distributed across the conveyor to prevent localized stress and potential damage.
- Implement Load Monitoring: Utilize load sensors and monitoring systems to detect and address overloading issues before they become problematic.
5. Dust and Debris Accumulation
Issue: Dust and debris can accumulate on the conveyor system, leading to decreased efficiency, increased wear, and potential safety hazards. This is particularly problematic in environments where dust is prevalent.
Prevention:
- Regular Cleaning: Implement a regular cleaning schedule to remove dust and debris from the conveyor system. This includes cleaning the belts, rollers, and other components.
- Enclosures and Covers: Use enclosures or covers to protect the conveyor system from dust and debris, especially in environments where dust is a significant issue.
- Proper Ventilation: Ensure that your facility has adequate ventilation to minimize the accumulation of dust and debris.
Conclusion
Maintaining a smooth and efficient conveyor system is essential for the success of any automotive manufacturing operation. By addressing these common issues—belt slippage, mechanical failures, accumulation problems, overloading, and dust and debris accumulation—you can minimize downtime, extend the lifespan of your equipment, and improve overall productivity.
Incorporating high-quality components from trusted brands like Omtec can further enhance your conveyor system’s performance. Their PBT-1 pop-up ball transfers, pop-up positioner pads, and Omtec Ball Transfer Tables provide reliable solutions to common conveyor problems, ensuring smooth operation and efficiency.
For top-notch conveyor components and expert solutions, visit AT Auto Conveyor. Our range of products, including pop-up ball transfers, Conveyor Platforms, and more, is designed to meet the highest standards of quality and performance. Ensure your conveyor system operates at its best by investing in reliable components and regular maintenance.
By taking proactive steps to prevent these common conveyor issues and utilizing high-quality solutions, you can achieve a more reliable and efficient production line, ultimately driving success in your automotive manufacturing operations.
Greetings! Very helpful advice on this article! It is the little changes that make the biggest changes. Thanks a lot for sharing!