Your cart is currently empty!
How to Choose the Right Size Mounting Stud
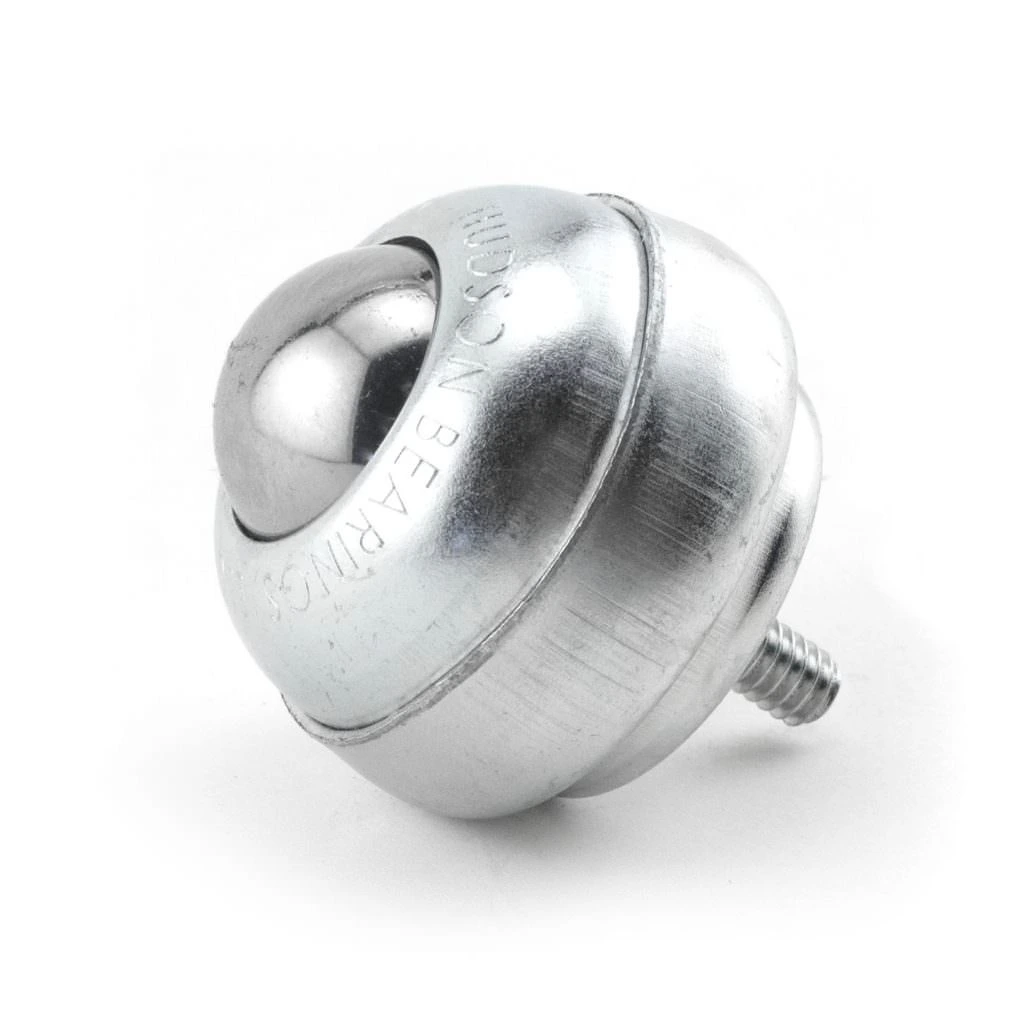
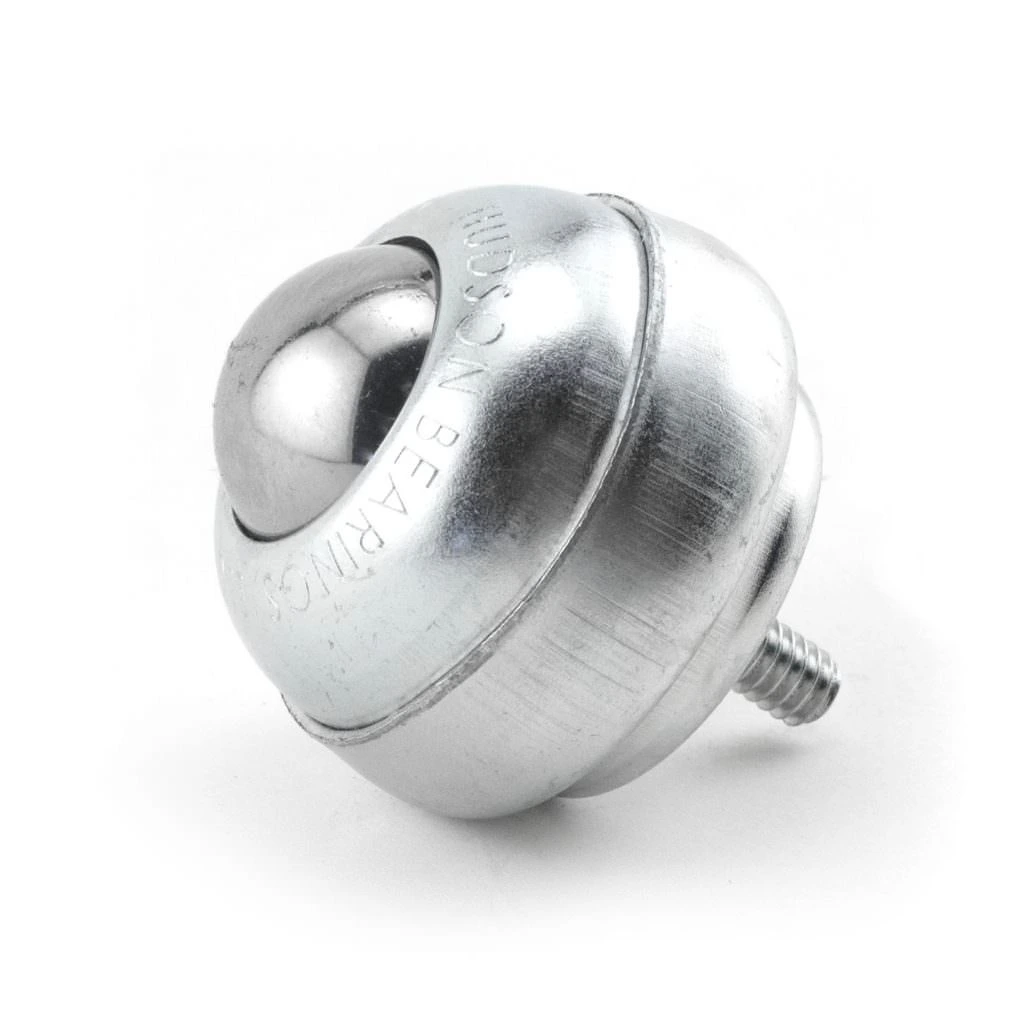
Ball transfer units (BTUs) are essential components in material handling, offering smooth multidirectional movement for a variety of applications, from conveyor systems to machine tools. Among the different types, stud-mounted ball transfer units are particularly popular due to their ease of installation and flexibility. However, choosing the right size mounting stud is critical for ensuring optimal performance, durability, and safety of the system.
In this blog post, we will explore the factors involved in choosing the right size mounting stud for stud-mounted ball transfer units, how to assess your application’s requirements, and why proper selection matters for both efficiency and long-term maintenance.
1. Understanding Ball Transfer Units and Their Applications
Ball transfer units are designed to support and move heavy objects with minimal effort. Each unit contains a large load-bearing ball, housed in a casing with multiple smaller support balls underneath, allowing for smooth omnidirectional movement.
Stud-mounted ball transfer units, as the name implies, come with a threaded stud that enables easy installation onto a surface by simply screwing it into place. These BTUs are commonly used in the following applications:
- Conveyor systems: for transferring products at junctions, corners, or where direction changes are needed.
- Assembly lines: for moving parts or components during the manufacturing process.
- Inspection stations: to easily reposition parts for quality checks or inspection.
- Packaging and sorting systems: for guiding and directing products efficiently.
In each of these applications, ensuring the ball transfer unit is securely mounted is crucial, and this requires selecting the correct size mounting stud.
2. Why Choosing the Right Size Mounting Stud Matters
Choosing the wrong size stud can lead to various issues, including reduced load capacity, instability, and increased wear on the ball transfer unit and surrounding equipment. On the other hand, the right stud size ensures:
- Secure Installation: The unit remains firmly attached to the mounting surface without any risk of loosening or failure.
- Optimal Load Distribution: A stud that is appropriately sized for the load ensures the BTU performs efficiently, evenly distributing weight and reducing strain on individual components.
- Durability and Longevity: Using the correct stud size reduces the likelihood of premature wear or damage, ensuring a longer lifespan for the unit and the equipment it supports.
- Safety: A stable, properly secured ball transfer unit minimizes the risk of accidents or malfunctions in high-stress or heavy-load applications.
3. Key Factors to Consider When Choosing the Mounting Stud Size
3.1 Load Capacity
The first and most important factor to consider is the load capacity of the ball transfer unit. The stud size must be strong enough to support the weight of the load being transferred, along with any dynamic forces that may occur during movement.
Manufacturers typically provide load ratings for their ball transfer units, which indicate the maximum weight they can safely support. For example, a BTU with a load capacity of 100 kg would require a stud size that can handle the same or greater load without bending, breaking, or becoming loose.
It’s important to account for any potential overloading that could occur during the operation. If the load is subject to frequent increases or fluctuates greatly, opting for a larger stud size with a higher load rating can help prevent failure.
3.2 Thread Size
The thread size of the stud is another critical factor. Thread sizes are usually specified in metric measurements (e.g., M6, M8, M10) or imperial measurements (e.g., ¼”, ⅜”, ½”). The size you choose must correspond to the mounting holes on the equipment or surface where the BTU will be installed.
- M6 to M8 (¼” to ⅜”): These are smaller thread sizes that are suitable for lighter loads and applications where space is limited, such as small packaging lines or light-duty conveyor systems.
- M10 to M12 (½”): These are medium-sized studs suitable for moderate loads, making them ideal for most industrial applications.
- M14 and larger (¾” or more): Larger thread sizes are designed for heavy-duty applications where the BTUs are expected to carry significant weight, such as in automotive or heavy machinery manufacturing.
3.3 Stud Length
The length of the mounting stud is equally important. The stud should be long enough to penetrate the mounting surface and secure the ball transfer unit, but not so long that it interferes with other components or the operation of the system.
When determining the appropriate stud length, consider:
- Thickness of the mounting surface: The stud must pass through the surface and allow for enough thread engagement to hold the BTU securely. For metal surfaces, the standard recommendation is to have at least two to three full turns of thread engagement. For wood or softer materials, more engagement may be needed.
- Clearance and space constraints: Make sure the stud does not protrude too far into areas where it might interfere with the operation of nearby equipment or cause safety issues.
3.4 Type of Mounting Surface
The type of material your ball transfer unit will be mounted on also influences the stud size. For example:
- Metal surfaces: Studs with finer threads are more suitable as they can provide a tighter fit. Thicker studs may be necessary for high-stress applications to prevent stripping of the threads.
- Wood or softer materials: Coarser threads provide better grip in softer materials, preventing the stud from pulling out over time.
- Concrete or masonry: Anchoring systems may be required in these cases, and the stud size must accommodate the type of anchor being used.
3.5 Environmental Considerations
Environmental conditions can affect the choice of both the ball transfer unit and its mounting stud. In corrosive environments, such as those exposed to chemicals, saltwater, or extreme weather conditions, stainless steel or zinc-coated studs should be used to prevent corrosion and ensure long-term performance.
4. Common Mistakes to Avoid
4.1 Using an Undersized Stud
Selecting a stud that is too small for the load can result in failure, leading to damage to the BTU, the conveyor system, or the materials being handled. Always refer to the manufacturer’s load ratings and ensure the stud matches the application’s requirements.
4.2 Ignoring Thread Compatibility
Mismatching the thread size of the stud with the mounting surface or the BTU can cause installation issues, from loose connections to stripped threads. Verify that the thread size of the stud is compatible with the mounting holes.
4.3 Overlooking Surface Thickness
If the stud is too short for the surface it’s being mounted on, the BTU may not be securely fastened, resulting in instability during operation. Make sure the stud length is appropriate for the thickness of the mounting material.
5. Steps to Choosing the Right Mounting Stud
Now that we’ve discussed the key factors, here’s a step-by-step process to guide you in selecting the correct size mounting stud for your stud-mounted ball transfer unit:
Step 1: Determine the Load Requirements
Identify the maximum load the BTU will need to support. Refer to the manufacturer’s specifications for the BTU’s load capacity and ensure the stud is strong enough to handle the load.
Step 2: Check the Thread Size
Verify the thread size required for the BTU. Check that the mounting surface can accommodate the same thread size for proper installation.
Step 3: Measure the Surface Thickness
Measure the thickness of the mounting surface and choose a stud length that will provide adequate engagement for a secure fit.
Step 4: Consider the Environment
If your BTUs will be exposed to harsh conditions, opt for corrosion-resistant materials like stainless steel or zinc-plated studs to ensure durability.
Step 5: Install and Test
Once the appropriate stud is selected, install the ball transfer unit and test its performance under typical operating conditions. Ensure the unit is securely mounted and performs as expected before full operation begins.
6. Conclusion
Choosing the right size mounting stud for stud-mounted ball transfer units is essential for ensuring efficient, reliable, and safe operation in any material handling or manufacturing application. By considering factors like load capacity, thread size, stud length, and environmental conditions, you can select the appropriate stud size for your specific needs. Proper installation and maintenance will not only prolong the life of your ball transfer units but also contribute to the overall success of your operation.