Your cart is currently empty!
Solutions To Down Time And Maintenance In Manufacturing Assembly Lines
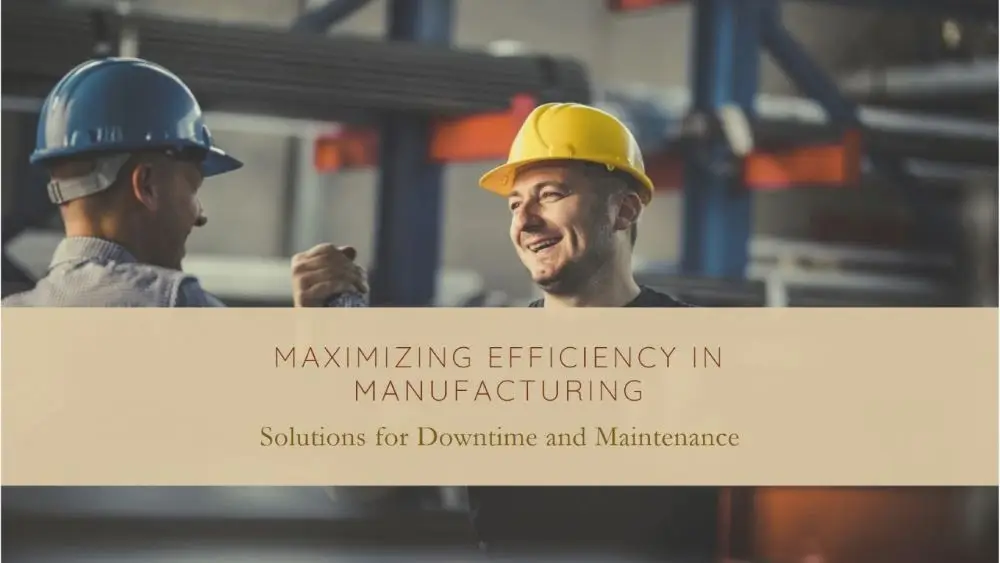
Manufacturing assembly lines are the backbone of modern production, driving efficiency and scalability in countless industries. However, one of the most significant challenges faced by these systems is downtime and maintenance. This blog post will delve into the root causes of downtime in assembly lines, explore its impact, and propose effective solutions, including the integration of Omtec ball transfers as a potential game-changer.
Understanding Downtime and Maintenance
What is Downtime?
Downtime refers to periods when a manufacturing assembly line is not operational due to various factors. It can be categorized into several types:
- Scheduled Downtime: Planned interruptions for routine maintenance, upgrades, or changeovers.
- Unscheduled Downtime: Unexpected interruptions caused by machine breakdowns, operational issues, or external factors.
- Minor Downtime: Short-term interruptions that may be due to small issues or quick fixes.
- Major Downtime: Extended periods of inactivity due to significant breakdowns or repairs.
Why Does Downtime Occur?
Downtime in assembly lines can arise from numerous factors:
- Equipment Failures: Machinery and components can fail due to wear and tear, malfunctions, or manufacturing defects.
- Human Error: Operator mistakes or inadequate training can lead to production stoppages. <— (Me right here) haha
- Supply Chain Issues: Delays or shortages in raw materials can halt production.
- Maintenance Scheduling: Inadequate planning or execution of scheduled maintenance can cause unexpected downtimes.
- System Failures: Issues with software or control systems can impact production efficiency.
Impact of Downtime
The effects of downtime are far-reaching and can severely impact a manufacturing operation:
- Financial Losses: Downtime directly affects productivity, leading to decreased output and potential revenue loss. The cost of repairs, maintenance, and replacement parts can also be significant.
- Decreased Productivity: Interruptions disrupt the flow of production, reducing overall efficiency and throughput.
- Quality Issues: Downtime can lead to inconsistencies in product quality, especially if repairs are rushed or if machinery is not properly calibrated.
- Customer Satisfaction: Delays in production can impact delivery schedules, affecting customer satisfaction and trust.
- Employee Morale: Frequent downtime can lead to frustration among workers, impacting morale and productivity.
Solutions to Minimize Downtime and Improve Maintenance
To effectively address downtime and maintenance issues, manufacturers must implement a range of strategies and solutions. Here’s a comprehensive approach to tackling these challenges:
1. Implement Predictive Maintenance
Predictive maintenance uses data analytics and monitoring technologies to predict when equipment is likely to fail, allowing for timely interventions before problems occur.
- Data Collection: Utilize sensors and IoT devices to collect data on equipment performance, including temperature, vibration, and usage.
- Analysis: Apply machine learning algorithms to analyze data and predict potential failures.
- Action: Schedule maintenance activities based on predictions rather than fixed intervals.
2. Adopt Preventive Maintenance Practices
Preventive maintenance involves regular, scheduled upkeep to prevent equipment failures and prolong the lifespan of machinery.
- Routine Inspections: Establish a regular schedule for inspecting and servicing equipment.
- Standard Operating Procedures: Develop and adhere to standard maintenance procedures to ensure consistency and effectiveness.
- Training: Train maintenance staff and operators on best practices for equipment care and troubleshooting.
3. Invest in Spare Parts Inventory
Maintaining an adequate inventory of critical spare parts can reduce downtime caused by waiting for parts to arrive.
- Inventory Management: Implement an inventory management system to track spare parts and ensure availability.
- Vendor Relationships: Develop strong relationships with suppliers to expedite parts procurement when needed.
- Critical Parts Identification: Identify and prioritize spare parts that are essential to the operation of the assembly line.
4. Improve Operator Training and Engagement
Well-trained operators are crucial to minimizing downtime and maintaining equipment.
- Training Programs: Develop comprehensive training programs for new and existing operators.
- Cross-Training: Cross-train operators to handle multiple tasks and respond to issues effectively.
- Feedback Mechanisms: Implement feedback mechanisms to gather insights from operators on potential issues and improvements.
5. Use Advanced Maintenance Technologies
Incorporate advanced technologies to enhance maintenance practices and reduce downtime.
- Condition Monitoring: Use condition monitoring tools to track the health of machinery in real-time.
- Remote Diagnostics: Implement remote diagnostic capabilities to troubleshoot and resolve issues without on-site visits.
- Automation: Integrate automation systems that can perform routine maintenance tasks or alert staff to potential issues.
6. Optimize Maintenance Scheduling
Efficient scheduling of maintenance activities can prevent unnecessary disruptions.
- Dynamic Scheduling: Use data-driven scheduling to align maintenance activities with production schedules and minimize disruptions.
- Downtime Planning: Plan maintenance activities during periods of low production demand or off-hours.
7. Enhance Communication and Coordination
Effective communication and coordination among maintenance teams, operators, and management are essential.
- Communication Channels: Establish clear communication channels for reporting and addressing issues.
- Coordination Meetings: Hold regular meetings to discuss maintenance schedules, issues, and improvements.
- Documentation: Maintain detailed records of maintenance activities, equipment performance, and downtime incidents.
8. Evaluate and Upgrade Equipment
Assess the performance and reliability of existing equipment and consider upgrades when necessary.
- Performance Assessment: Regularly evaluate equipment performance to identify areas for improvement.
- Modernization: Invest in newer, more reliable machinery that offers improved performance and lower maintenance requirements.
The Role of Omtec Ball Transfers in Reducing Downtime
One innovative solution to address downtime and maintenance issues in manufacturing assembly lines is the use of Omtec ball transfers. These devices can play a crucial role in enhancing the efficiency and reliability of assembly line operations.
What are Omtec Ball Transfers?
Omtec ball transfers are mechanical components designed to facilitate the smooth movement of materials and products along an assembly line. They consist of a series of ball bearings housed in a rotating mechanism, allowing for easy and low-friction movement of items.
Benefits of Omtec Ball Transfers
- Reduced Friction and Wear: Omtec ball transfers minimize friction between moving parts, reducing wear and tear on equipment and components.
- Improved Load Handling: These devices are designed to handle various loads and weights, providing reliable performance in diverse applications.
- Enhanced Durability: Omtec ball transfers are built to withstand harsh conditions and continuous use, reducing the frequency of replacements and repairs.
- Ease of Installation and Maintenance: They are relatively easy to install and maintain, contributing to lower downtime and maintenance costs.
- Versatility: Ball transfers can be used in a wide range of applications, from conveyor systems to workstations, offering flexibility and adaptability.
Implementing Omtec Ball Transfers
To leverage the benefits of Omtec ball transfers, consider the following steps:
- Assessment: Evaluate the current assembly line setup to identify areas where ball transfers could improve performance.
- Integration: Integrate ball transfers into existing conveyor systems, workstations, or other critical points in the assembly line.
- Training: Train maintenance staff and operators on the proper use and maintenance of ball transfers.
- Monitoring: Continuously monitor the performance of ball transfers to ensure they are operating effectively and address any issues promptly.
Conclusion
Downtime and maintenance issues are significant challenges in manufacturing assembly lines, impacting productivity, quality, and overall efficiency. By adopting strategies such as predictive and preventive maintenance, improving training, investing in spare parts, and leveraging advanced technologies, manufacturers can effectively address these challenges.
The integration of Omtec ball transfers offers a promising solution to enhance the efficiency and reliability of assembly lines. By reducing friction, improving load handling, and enhancing durability, ball transfers can play a crucial role in minimizing downtime and maintenance costs. Check them out here… Omte Corp Pneumatic & Fixed Ball Transfer Units (atautoconveyor.com)
As manufacturing continues to evolve, embracing innovative solutions and best practices will be key to maintaining competitive advantage and ensuring the smooth operation of assembly lines. By proactively addressing downtime and maintenance issues, manufacturers can achieve greater efficiency, higher quality, and increased customer satisfaction.
My brother suggested I might like this blog. He was entirely right. This post actually made my day. You cann’t imagine simply how a lot time I had spent for this information! Thanks!