Your cart is currently empty!
Overcoming Common Pain Points in Manufacturing: Strategies for Success
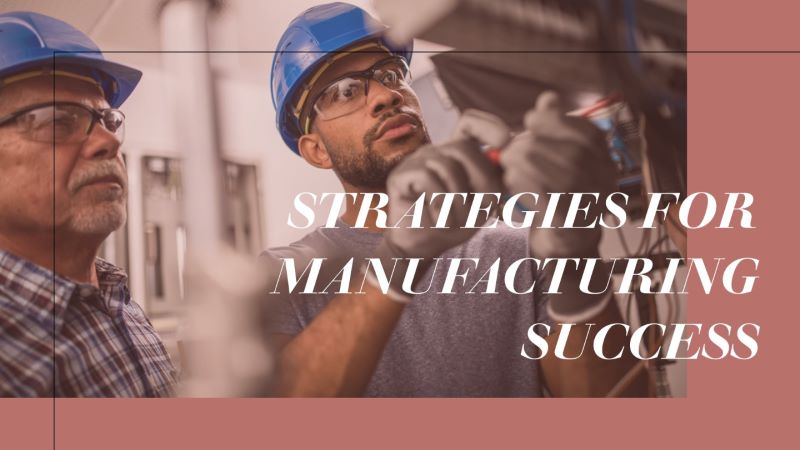
Challenges in Production Processes
The manufacturing sector is the backbone of global industry, driving innovation, production, and economic growth. However, this critical sector also faces a variety of pain points that can hinder efficiency, productivity, and profitability. Understanding these challenges and implementing effective solutions is crucial for manufacturing companies striving to stay competitive in an ever-evolving market. In this blog post, we will explore some of the most common pain points in manufacturing and offer strategies to address them.
1. Inefficient Processes
Pain Point:
Manufacturing processes can often become inefficient due to outdated machinery, manual workflows, and lack of standardization. Inefficiency leads to increased production times, higher costs, and reduced output quality.
Solution:
Automation and Technology Integration:Investing in modern machinery and automation technologies can significantly enhance production efficiency. Automated systems reduce the need for manual intervention, minimize errors, and streamline workflows. Implementing technologies such as robotics, Internet of Things (IoT), and advanced manufacturing software can optimize production lines and improve overall efficiency.
Lean Manufacturing Principles:Adopting lean manufacturing principles, such as just-in-time (JIT) production and continuous improvement (Kaizen), helps eliminate waste and improve process flow. Regularly reviewing and refining processes ensures that inefficiencies are identified and addressed promptly.
2. Supply Chain Disruptions
Pain Point:
Supply chain disruptions, whether due to natural disasters, geopolitical tensions, or pandemics, can severely impact manufacturing operations. Delays in receiving raw materials and components can halt production and lead to missed deadlines.
Solution:
Diversified Supply Chain:Building a diversified supply chain with multiple suppliers reduces dependency on a single source. This approach provides flexibility and resilience in the face of disruptions. Establishing relationships with local and international suppliers ensures a steady flow of materials.
Advanced Planning and Inventory Management:Implementing advanced planning and inventory management systems enables manufacturers to anticipate potential disruptions and plan accordingly. Technologies such as predictive analytics and AI can forecast demand and optimize inventory levels, ensuring materials are available when needed.
3. Quality Control Issues
Pain Point:
Maintaining consistent quality is crucial in manufacturing. Quality control issues can lead to defective products, increased returns, and damage to the company’s reputation.
Solution:
Quality Management Systems (QMS):Implementing a robust Quality Management System (QMS) ensures that quality standards are consistently met. QMS includes processes for monitoring, measuring, and improving product quality. Regular audits and inspections help identify and rectify issues before they escalate.
Training and Employee Engagement:Investing in employee training and fostering a culture of quality within the organization is vital. Well-trained employees are more likely to adhere to quality standards and identify potential issues early. Encouraging employee engagement and feedback can lead to continuous improvement in quality control processes.
4. Workforce Challenges
Pain Point:
Manufacturing companies often face challenges related to workforce management, including labor shortages, skill gaps, and high turnover rates.
Solution:
Attractive Workforce Policies:Creating a positive work environment with competitive wages, benefits, and opportunities for career growth can attract and retain skilled workers. Offering flexible work arrangements and ensuring a safe workplace are also crucial.
Training and Development Programs:Implementing comprehensive training and development programs helps bridge skill gaps and ensures employees are equipped with the necessary knowledge and expertise. Partnerships with educational institutions and apprenticeships can also provide a pipeline of skilled workers.
Automation and Augmentation:Integrating automation and augmented reality (AR) technologies can help mitigate workforce challenges. Automation can handle repetitive and labor-intensive tasks, allowing human workers to focus on more complex and value-added activities. AR can provide real-time guidance and training, enhancing workforce productivity.
5. Cost Management
Pain Point:
Managing costs effectively is a perennial challenge for manufacturing companies. Rising raw material prices, energy costs, and labor expenses can erode profit margins.
Solution:
Cost Analysis and Optimization:Conducting regular cost analysis helps identify areas where expenses can be reduced without compromising quality. Implementing cost optimization strategies, such as renegotiating supplier contracts, adopting energy-efficient practices, and streamlining processes, can lead to significant savings.
Technology and Innovation:Investing in innovative technologies, such as additive manufacturing (3D printing) and IoT, can reduce production costs. These technologies enable manufacturers to produce complex components more efficiently and with less material waste.
6. Regulatory Compliance
Pain Point:
Manufacturing companies must navigate a complex landscape of regulations and standards. Non-compliance can result in hefty fines, legal issues, and reputational damage.
Solution:
Compliance Management Systems:Implementing comprehensive compliance management systems ensures that all regulatory requirements are met. These systems monitor changes in regulations, track compliance status, and generate reports for audits.
Employee Training and Awareness:Regular training sessions on regulatory compliance are essential for all employees. Ensuring that employees understand the importance of compliance and the specific requirements related to their roles reduces the risk of non-compliance.
7. Sustainability and Environmental Impact
Pain Point:
Increasing pressure from consumers, governments, and stakeholders to adopt sustainable practices presents a significant challenge. Manufacturing processes often have substantial environmental impacts, including high energy consumption and waste generation.
Solution:
Sustainable Manufacturing Practices:Implementing sustainable manufacturing practices, such as using renewable energy sources, reducing waste, and optimizing resource usage, can minimize environmental impact. Embracing circular economy principles, such as recycling and reusing materials, also contributes to sustainability.
Green Certifications:Obtaining green certifications, such as ISO 14001, demonstrates a commitment to environmental responsibility. These certifications enhance the company’s reputation and can provide a competitive advantage in the market.
8. Customer Demand and Market Fluctuations
Pain Point:
Fluctuations in customer demand and market conditions can create challenges in maintaining production levels and managing inventory.
Solution:
Demand Forecasting and Flexibility:Implementing advanced demand forecasting tools helps predict market trends and customer preferences. Being flexible in production planning and maintaining a buffer inventory can help manage fluctuations effectively.
Customer Relationship Management (CRM):Using CRM systems to gather customer insights and feedback enables manufacturers to respond quickly to changing demands. Understanding customer needs and preferences helps tailor production and marketing strategies accordingly.
9. Technology Adoption and Integration
Pain Point:
The rapid pace of technological advancement can be daunting for manufacturing companies. Integrating new technologies into existing systems without disrupting operations is a significant challenge.
Solution:
Strategic Technology Roadmap:Developing a strategic technology roadmap guides the adoption and integration of new technologies. This roadmap should align with the company’s overall business strategy and include clear milestones and timelines.
Pilot Projects and Scaling:Implementing pilot projects allows companies to test new technologies on a small scale before full deployment. Evaluating the results and making necessary adjustments ensures smooth integration. Once proven successful, the technology can be scaled across the organization.
10. Cybersecurity Threats
Pain Point:
As manufacturing companies become increasingly reliant on digital technologies, they become more vulnerable to cybersecurity threats. Cyberattacks can disrupt operations, compromise sensitive data, and damage the company’s reputation.
Solution:
Robust Cybersecurity Measures:Implementing robust cybersecurity measures, such as firewalls, encryption, and multi-factor authentication, protects against cyber threats. Regular security audits and updates ensure that systems remain secure.
Employee Training and Awareness:Training employees on cybersecurity best practices and the importance of data protection is crucial. Ensuring that employees recognize potential threats and know how to respond minimizes the risk of cyberattacks.
Conclusion
Manufacturing companies face a myriad of challenges that can impede their efficiency, productivity, and profitability. However, by understanding these pain points and implementing effective solutions, manufacturers can overcome these obstacles and thrive in a competitive market. Embracing automation, diversifying supply chains, investing in employee training, and adopting sustainable practices are just a few strategies that can drive success. By staying agile and proactive, manufacturing companies can navigate challenges and continue to be the backbone of global industry.